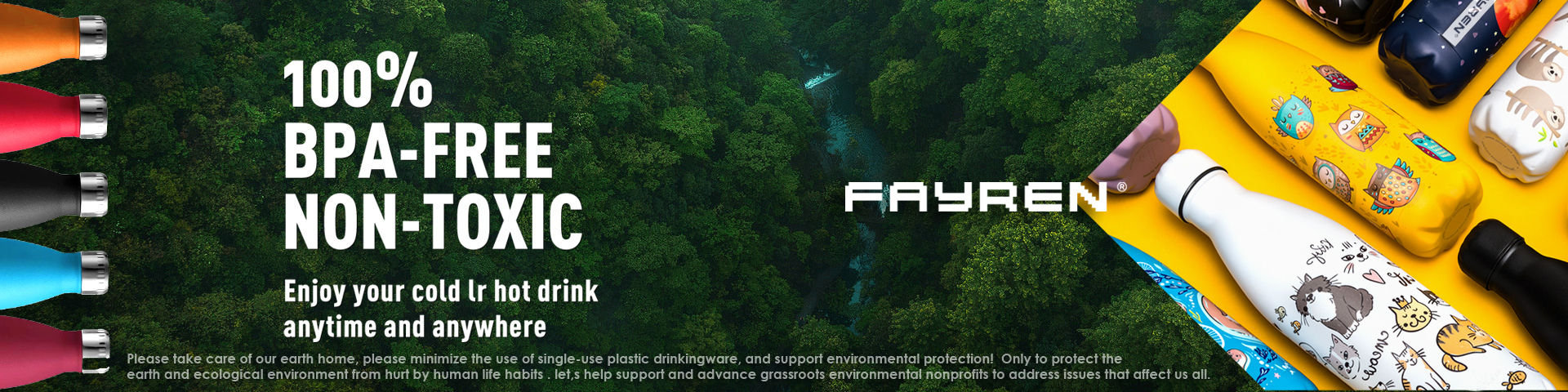
How do water bottle manufacturers ensure that they meet these standards?
2024-07-22 17:35
Water bottle manufacturers employ various strategies to ensure they meet quality and safety standards for their products.
Here are some of the key practices they follow:
1
Material Sourcing and Verification:
Manufacturers carefully select stainless steel suppliers that can provide materials meeting the required chemical composition, mechanical properties, and surface finish standards.
They conduct extensive testing and verification of the incoming raw materials to ensure compliance with industry and regulatory requirements.
This includes analyzing the steel's chromium, nickel, and other alloying element content to confirm it meets the specifications for food-grade stainless steel water bottle.
2
Production Process Controls:
Manufacturers implement strict process controls throughout the production line, including:
Dimensional checks to ensure water bottles are within the specified tolerances for height, diameter, wall thickness, etc.
Surface finish inspections to identify any scratches, dents, or other visual defects.
Leak testing to verify the sports drinking bottles are leak-proof and can withstand intended use conditions.
Functionality testing, such as drop tests, to ensure the insulated water bottles can withstand normal wear and tear.
They often use statistical process control (SPC) techniques to monitor and maintain consistent product quality.
3
Third-Party Certification and Audits:
Many water bottle stainless steel manufacturers seek third-party certifications, such as ISO 9001 (quality management) and SEDEX, to demonstrate their commitment to quality and safety.
These certifications require regular audits by independent bodies to verify that the manufacturer's quality management system and production processes meet the established standards.
4
Regulatory Compliance:
Water bottle manufacturers must comply with relevant regulations and guidelines, such as those set by the U.S. Food and Drug Administration (FDA) for food contact materials.
They ensure that the materials, coatings, and any other components used in the bottle design are approved for food contact and do not pose health risks.
Manufacturers often work closely with regulatory authorities to stay informed of any updates or changes in the relevant standards and guidelines.
5
Quality Assurance Sampling and Testing:
Manufacturers implement comprehensive quality assurance (QA) programs that involve regular sampling and testing of finished products.
This includes physical, chemical, and microbiological tests to verify compliance with quality and safety specifications.
The QA team may also conduct accelerated aging tests to evaluate the long-term performance and durability of the vacuum flask.
6
Traceability and Recall Preparedness:
Manufacturers maintain detailed records and traceability systems to track the source of materials, production batches, and distribution of their metal water bottles.
This allows them to quickly identify and isolate any potentially defective or non-compliant products and initiate targeted recalls if necessary.
By implementing these robust quality control and assurance measures, water bottle manufacturers can ensure their products meet the required standards for safety, performance, and customer satisfaction.
Get the latest price? We'll respond as soon as possible(within 12 hours)